Два способа применения эпоксилина
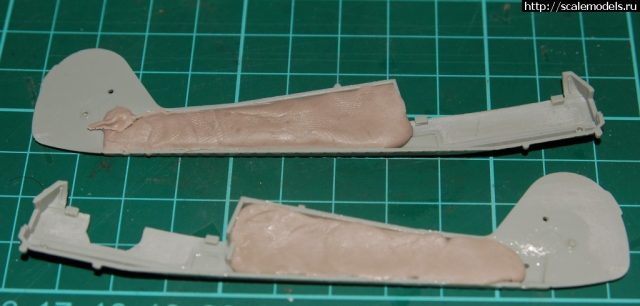
Одним из самых перспективных и широко распространенных направлений усовершенствования промышленного полистиролового набора всеми признается добавление к нему различных деталей, находящихся внутри образца техники и видимых через открытые капоты, люки и лючки, фонарь кабины, в нишах шасси и т.д.
Способ первый – делаем слепок внутренностей
В некоторых случаях, чтобы показать внутреннее устройство прототипа, не грех сделать часть обшивки из прозрачного материала. Но при таких доработках модели возникает трудность: новые самодельные детали должны соответствовать размерам имеющихся полостей и повторять их форму. Если эта форма сложна (а применительно к авиации так чаще всего и бывает), то встает вопрос о ее снятии и переносе на рабочий чертеж, тот самый scratch, с которого потом будет build.
Чертежи прототипа нам помогут мало: стенки полистироловой модели гораздо толще самолетной обшивки и, соответственно, все самолетные внутренности, чтобы уместиться в объем между ними, должны быть выполнены в заметно меньшем масштабе. Например, предположим, что у нас есть модель самолета в масштабе 1:72 и ее капот имеет ширину 10 мм. Если полистироловые стенки имеют толщину 0,75 мм (очень даже скромно), то пространство внутри капота «ужмется» до масштаба 1:85. При этом кабина пилотов (ширина, условно, 3 см) пострадает в масштабе значительно меньше. При прочих равных ее можно будет выполнить в масштабе 1:76 или просто разместить все, что там должно быть, несколько плотнее, чем положено, авось пластиковые пилоты на тесноту жаловаться не станут. И это мы рассмотрели пока только одно измерение, а их три, и по всем будут чуть-чуть разные масштабы. Так что, как ни крути, а чертеж модели неминуемо будет весьма серьезно отличаться от чертежа прототипа, тем более, что и материалы, имеющиеся в нашем распоряжении, накладывают свои ограничения. Надо, например, куда-то девать толщину листовых полистироловых деталей. Даже если это – бронеспинка, то она же не 72 миллиметра толщиной, и даже не 36. Итак, нам нужен свой чертеж, а он начинается со снятия размеров.
Майк Эши (Mike Ashey) в своей, не побоюсь этого слова, классической работе «Model aircraft tips and techniques» предлагает на выбор три способа решения данной проблемы:
- Приобрести кит в двух экземплярах, из коих один разрезать на куски и снять требуемые сечения с натуры. Этот способ я, по понятным причинам, отмёл.
- Воспользоваться штырьковым шаблоном для снятия профилей. Эта идея выглядит лучше, но все равно не настолько хорошо, чтобы сразу и безоговорочно ее принять. Во-первых, у меня нет такого инструмента, и я не знаю, где бы его купить. Те, кто брался его привезти в наш стольный град, запрашивали дурные деньги и, к тому же, заказ брали на «после дождика в четверг». Во-вторых, и это самое главное, такой способ не может быть слишком точен. Точность штырькового шаблона определяется толщиной штырьков, а она, по соображениям прочности, не может быть слишком мала. Для нас же неточность в несколько десятых миллиметра уже неприемлема.
- Загерметизировать внутренности модели и налить в нее эпоксидки, а затем, распиливая эту отливку, получать искомые сечения.
Этот способ показался мне наиболее перспективным, но Эши предупредил о его подводных камнях:
Во-первых, требуется не только герметически закрыть щель между деталями, но и полностью ее уничтожить и при этом не деформировать детали. Если она останется, то и сечение, полученное таким способом, будет шире действительного. А такое оно нам зачем?
Во-вторых, эпоксидная смола, полимеризуясь, выделяет тепло и это тепло в состоянии деформировать пластик. Может быть, для 72-го масштаба проблема надумана, но проверять у меня не было вдохновения.
В-третьих, у меня возникли сомнения в собственной способности покрыть разделительным слоем все поверхности, до которых может добраться эпоксидка. Я, конечно, купил модель, чтобы ее склеить, но не на этом этапе.
Наконец, в-четвертых, требовал решения вопрос, как залить смолу именно туда, где она требуется, да еще и чтобы без пузырей. Как назло, оба объема, которые я собирался детализировать, имели узкие и неудобные отверстия, а выпиливать в пластике люки я не хотел до того, как удостоверюсь в своей способности сделать приличный интерьер.
Все эти опасения сподвигли меня задуматься, чем можно без ущерба для дела заменить смолу. Решение нашлось в упаковке с «Эпоксилином». Это не жидкость, а пластичная масса и никуда, куда не надо, она не утечет. Правда, куда надо она не потечет тоже, но ее можно заложить внутрь формы до соединения половин. Здесь и далее под формой мы будем понимать пару пластиковых деталей, образующих объем, который требуется снять: фюзеляж, крыло, мотогондолу и т.д. Липкость эпоксилина гораздо ниже, чем у клеев, а на определенном этапе полимеризации и вовсе падает до нуля, так что шансы на благополучное разделение половин формы и извлечение слепка, соответственно выше. Наконец, пластические эпоксидные шпаклевки чуть менее чем полностью состоят из инертного наполнителя и, соответственно, тепла при отвердевании производят немного. Прочие виды двухкомпонентных шпаклевок, я думаю, можно использовать с не худшим результатом.
После пары экспериментов я разработал следующую технологию получения эпоксилиновых слепков.
В качестве разделительного слоя я использовал вазелин. В аптеке был приобретен тюбик, на котором так и написано «Вазелин для рук». Этим вазелином с помощью уховертки я протер внутренние поверхности формы, добиваясь того, чтобы они жирно блестели, но при этом видимых комков вазелина не было. Этим же вазелином смазываем руки, чтобы к ним не прилипал эпоксилин.
После этого нужно было заполнить форму эпоксилином. Итак, необходимый кусочек эпоксилина отрезан и размят. Первым делом отщипываем от него небольшой фрагмент, размером, скажем, с горошину, и откладываем. Он нам пока не понадобится, а впредь послужит индикатором зрелости слепка. Теперь отделяем небольшие кусочки эпоксилина и вдавливаем в те места, точная передача которых нам наиболее важна: углубленные ребра и углы, отверстия, приливы для крепления других деталей. Далее нетолстым слоем накладываем эпоксилин на всю поверхность и, опять же, вминаем внутрь формы, чтобы он заполнил все углубления. Наконец, заполняем остаток объема формы, чтобы эпоксилин чуть-чуть выступал над ее поверхностью и проделываем то же самое с ее второй половиной.
У меня модель небольшая и экономить эпоксилин не было смысла, но при работе с большими объемами представляется целесообразным заранее вырезать болванку, заполняющую большую часть объема слепка, а эпоксилином заполнить только промежутки между нею и формой. Эпоксилин можно замешивать в несколько приемов. В худшем случае, по линии соединения слоев в этом случае получатся чуть заметные следы. Для тех целей, которые стоят перед нами, это несущественно. Если нас интересует конкретный фрагмент объема, например поперечное сечение фюзеляжа в месте, где следует быть шпангоуту, нет необходимости тратить эпоксилин за его пределами. Наоборот, даже лучше, если ему есть куда вытесняться при соединении половин. В этом случае достаточно налепить эпоксилиновую «лепешку» или «колбаску» на интересующее место.
Теперь нам нужно аккуратно соединить половинки формы. Дело это не хитрое, но есть пару тонкостей. Незастывший эпоксилин текуч и под давлением вытесняется в свободные объемы формы или за ее пределы, но процесс этот идет медленно. Если под давлением половинки формы сближаются, не надо усиливать его, пользы не будет, и так все получится. Во-вторых, нужно перед контактом между половинками формы позиционировать их как можно точнее, поскольку после контакта движения в плоскости стыка так же затруднены. Наконец, раздавить заполненную эпоксилином пластмассовую деталь очень непросто, можно этого не опасаться. Но если она заполнена не целиком, то усилие сжатия нужно прилагать именно к месту, где лежит эпоксилин, а не к краям, иначе можно-таки деформировать деталь.
Соединив половинки и убрав вытесненный наужу эпоксилин, нужно отложить форму и индикаторный кусочек на некоторое время. Для ускорения процесса можно положить их, например, на батарею. Через некоторое время (у меня, примерно, 1 час) наступит момент, когда пробный кусочек, при постукивании по нему, уже издает звонкий звук, но еще легко протыкается лезвием ножа. Самое время извлекать слепок.
Форму разделяем лезвием ножа, раздвигая половинки то с одной, то с другой стороны. Пластиковые детали, которые сами отливают в форме, устроены так, что их внутренние стенки всегда имеют хоть небольшой, но уклон, поэтому, достаточно раздвинуть половинки формы на миллиметр-другой, чтобы одна из половин отвалилась, а слепок остался во второй.
Опять пускаем в ход нож, втыкаем его кончик в слепок и, действуя как рычагом, вынимаем его. Если слепок тонкий, то велика вероятность, что он при этом погнется.
Но риска в этом нет: на этой стадии затвердевания эпоксилин уже набрал достаточную прочность, чтобы не развалиться. Осмотрев слепок и убедившись, что он годится в дело, его просто укладывают обратно в форму и дают окончательно затвердеть. Это примерно сутки.
Предварительным разделением формы (мы его только что проделалали) пренебрегать не советую. Всегда есть риск, что в форме образовалась какая-нибудь царапина, создающая поднутрение или эпоксилин приклеился к пластику. Разделяя их своевременно, мы гарантируем, что слепок удастся выковырять хоть как-то. А если он вышел из формы один раз, то выйдет и второй, никуда не денется.
Ну, а после того, как слепок затвердел окончательно, осталось самое простое: определить интересующие нас сечения, разрезать по ним пилкой, приложить к листу бумаги и обвести. Чертеж чертежом, а если нужно изготовить, например, шпангоут, то, для точности, рекомендую размечать пластик не по чертежу, а непосредственно по слепку, обводя его чертилкой.
На фото ниже можно видеть конечный результат деталировки: ферменную конструкцию фюзеляжа и уложенные в багажный отсек пожитки немецкого связного пилота, которые дальновидный фриц возил с собой на случай ночевки вне своего аэродрома или аварийной посадки в пустыне. На готовой модели это хозяйство видно через открытый багажный люк в другой половине фюзеляжа.
Вместо того, чтобы по эпоксилиновым сечениям делать детали из листового пластика, в определенных обстоятельствах имеет смысл использовать в конструкции модели непосредственно части эпоксилинового слепка. Например, под брюхом истребителя Bf-110 помещается отсек, в котором установлены две автоматические пушки MG-151-20, а от их дул к портам в носовом обтекателе идут специальные толстые трубы. Помимо пропуска снарядов, они также служат для подачи к пушкам охлаждающего воздуха. Я задался целью сымитировать все это хозяйство в 72-м масштабе. Вот как оно выглядит та настоящей машине, выставленной в музее RAF:
Фотографии взяты из альбома Walk Around №24 Messerschmitt Bf-110G издательства Squadron/Signal.
Кроме того, замечу, что добраться до этих пушек можно не только через люк на нижней поверхности фюзеляжа, а и из кабины, через люк в ногах у радиооператора. Его я тоже хотел выполнить открытым. Обычно в таких случаях из листового пластика изготовляют стенки моделируемого отсека, и наполняют его соответствующим оборудованием. В нашем случае это смоляные макеты пушек MG-151 от фирмы Aires, патронные ленты, кабели и трубопроводы и т.д. А для того, чтобы вырезать пластиковые стенки нужно узнать их контуры, а для этого – снять профиль…
Я поступил проще: объем ниши был вырезан непосредственно в эпоксилиновом массиве. Вот как это выглядело:
Эпоксилиновый слепок в изначальном виде. Выступ в носовой части предназначен для получения профиля бронешпангоута, отделяющего кабину пилотов от отсека носовых пушек.
Затем было отрезано все лишнее, толщина оставшейся части слепка выведена шлифовкой сообразно размерам фюзеляжа и кабины пилотов, которая должна помещаться над ним, размечены и вырезаны объемы ниш для пушек и труб. В отсеке вооружения установлены пластиковые шпангоуты, форма заделана заподлицо с эпоксилиновым слепком, в половинках фюзеляжа проделаны вырезы. Трубы изготовлены из отрезков инъекционной иглы 18G. Все собрано предварительно, для демонстрации. Детали еще не скреплены, поэтому много что торчит криво, а некоторые мелочи еще не изготовлены вовсе.
Способ второй – закрепляем деталь для обработки
Все слыхали слово «перепил». То есть обработка резанием, будь то напильник, пила, сверло, абразивный материал или резец. Способ не новый, хорошо изученный. Резанием люди обрабатывают и обрабатывали разные материалы – от мамонтовых шкур до алмазов включительно. И практически во всяком ремесле, сопряженном с этим делом, есть железное правило: закрепи заготовку, потом подступай к ней с долотом либо напильником. Двумя руками и направлять инструмент легче и вести его можно точнее.
Придуманы и всевозможные приспособления, в которых следует закреплять заготовку. Почему же моделист в абсолютном большинстве случаев держит ее в пальцах, манипулируя ножом в опасной близости от них? Да потому, что подходящего средства для надежного закрепления пластиковых деталей до сих пор не было найдено. Задача двоякая: с одной стороны хрупкую пластиковую деталь нужно зажать так, чтобы она и шелохнуться не могла, с другой – не раздавить. Добавим к тому же, что чаще всего дорабатывать или изготовлять заново требуется мелкие и тонкие детали, которые и уцепить-то проблема, и именно потому, что они мелкие и тонкие и производитель поленился доводить их до ума. А нужно еще и обеспечить пространство для работы вокруг того фрагмента, который требуется доработать. Совсем хорошо, если деталь при этом можно будет поворачивать в наиболее удобное для очередной операции положение.
Не похвалюсь, что закрываю вопрос на веки вечные, но в определенных случаях предлагаемые способы могут быть полезны. Общее в них то, что по вышеописанной технологии с детали делается эпоксилиновый слепок, который, поскольку идеально повторяет форму детали, распределяет усилия, возникающие при механической обработке, на возможно большую площадь. Немаловажно, что эпоксилин тоже легко поддается механической обработке и в определенных обстоятельствах целесообразно резать или сверлить деталь прямо вместе со слепком.
Собственно, способ я открыл случайно. Снимая по предыдущему методу слепок с подкапотного пространства «Физелер шторха», я обнаружил, что половинка капота, во-первых, сидит на нем как влитая (а почему «как»?), а во-вторых – совершенно не пружинит наощупь. Поэтому, когда дело дошло до пиления, я, не мудрствуя лукаво, насадил одну из пластиковых половин на слепок, а остаток слепка зажал в тиски. И, ура-ура, обрел способность поворачивать деталь как мне удобно (тиски у меня шаровые), намертво фиксировать ее в этом положении и свободные руки.
На схемах приведены некоторые варианты закрепления деталей разной конфигурации для обработки. Сами детали обозначены зеленым, а эпоксилин – бледно-розовым. Обратите внимание на мягкие прокладки на губках тисок.
А — парная деталь в форме оболочки. При наличии наполнителя внутри, эта оболочка не раздавится даже при весьма сильном сжатии. Типичнейший случай для основных составляющих модели: фюзеляжа, крыла, подвесных баков и т.д. и т.п.
Б — Одиночная деталь в форме оболочки, например фонарь (см. ниже) Шуруп, замоноличенный в эпоксилин, предназначен для лучшего сцепления эпоксилинового слепка и технологической держалки. При достаточной площади соединения он не нужен.
В – Тонкая и, следовательно, хрупкая деталь зажата между двумя сделанными с нее половинными формами. Методика их получения примерно соответствует изготовлению классических разъемных гипсовых форм.
Г – Одинарная форма в виде ложемента.
Рассмотрим еще один живой пример, соответствующий схеме «Б»: подготовку вакуумформованного фонаря для того же «нахтягера» Bf-110. Австралийская фирма «Squadron» продает такие вакушки наборами: десяток фонарей для разных машин оттиснуты на одном листе пластика. Оттиснуты, замечу, очень даже тонко и аккуратно. Допустив брак в одном из фонарей, производители приложили исправный, вырезанный из другого листа.
Но вернемся к делу. Вырезать требуемый фонарь вчерне – дело не хитрое. А дальше начинаются трудности. Требуется:
- Вывести довольно сложную поверхность, по которой он соединяется с корпусом;
- Выбрать в хвостовой части амбразуру для пулемета;
- Просверлить отверстия для мачты антенны и установки schräge Musik;
- Распилить, получив люки пилота и хвостового стрелка с радиооператором. Всего нам требуется 7 фрагментов, для чего предстоит сделать 9 разрезов.
Одним словом – пилить и пилить. Может ли помочь делу эпоксилин? Разумеется, но примем во внимание, что заново отполировать фонарь из ПЭТ (материал, идущий на пластиковые бутылки) проблематично. Проще приложить все силы к тому, чтобы не исцарапать и не испачкать его. Поэтому в качестве разделительного слоя мы используем не вазелин, а тонкую пленку, в которую заворачивают бутерброды. Качество передачи деталей в слепке упало, но оно нам и не нужно. Гораздо важнее полная защищенность детали от следов эпоксилина. Увы, упала и надежность сцепления, это хуже. Пришлось на последних этапах обработки обмотать фонарь и слепок скотчем. Нет худа без добра, скотч послужил дополнительной защитой от царапин. К сожалению, до того, как эта идея пришла мне в голову, я успел царапнуть фонарь буром. Сделаем вид, что это – повреждение на реальной машине и так типа и должно быть. В конце концов, если весь самолет царапается, то с чего фонарю составлять исключение?
Для экономии эпоксилина внутрь слепка был вложен кусочек ламината примерно 8×8×25 мм и все положено отверждаться.
Могу сказать, что опыт в целом удался. На такой оправке вакушка исправно резалась пилкой и ножом, сверлилась, фрезеровалась бором (пулеметная амбразура) и шлифовалась по краю.
После выведения шлифовкой нижней плоскости фонаря, к ней был подклеен еще один кусочек дерева, позволяющий зажимать оправку в тиски.
Результат можно видеть на фото. Фонарь до резки на фрагменты и болванка:
Отверстия под установку schräge Musik еще не просверлены, тут требуется сделать эту самую установку и разметить отверстия по месту. Кстати, все разметочные построения можно делать на поверхности эпоксилиновой болванки, а на поверхности фонаря накалывать только центры отверстий, ориентируясь на видимую разметку. Если бы мы работали с непрозрачной деталью, то эпоксилиновую болванку можно было бы просверлить насквозь и использовать в качестве сверлильного кондуктора. В остальном технология не отличалась от предыдущего случая: кормовой фрагмент был наложен на болванку, закреплен скотчем и просверлен с нею вместе. Вот что получилось, примерка:
Вышеописанное изготовление технологической оснастки из эпоксилина – решение не универсальное и не всегда целесообразное по деньгам и трудозатратам. Но в определенных, причем, ИМХО, сложнейших случаях – это выход.
Источник